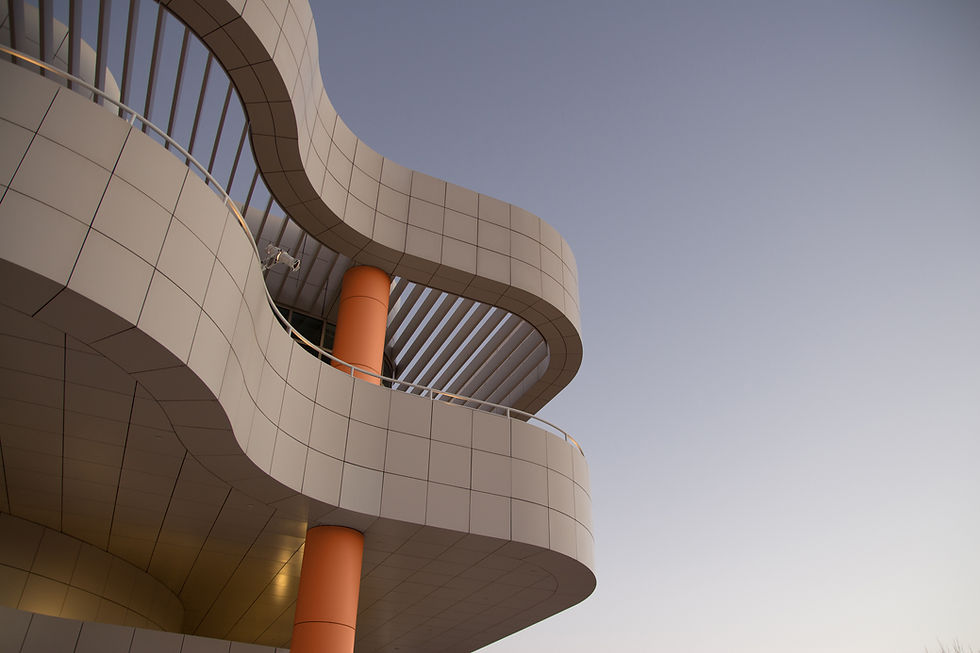
In the high-performance luxury catamaran market, shipyards are expected to deliver precision, innovation, and flawless execution. But behind the sleek lines and cutting-edge design, even the most respected builders can face complex internal challenges. This case study explores how one renowned shipyard, specializing in custom luxury performance catamarans, confronted and began addressing core operational inefficiencies that were hindering their production and warranty workflows.
Background
This Asian-based shipyard has earned a reputation for blending bespoke craftsmanship with performance engineering. Each catamaran is a one-of-a-kind creation, tailored to the client’s vision, and built for both bluewater cruising and high-speed passage-making. While their product speaks to innovation and excellence, the internal systems powering the day-to-day operations were growing increasingly strained under the weight of complexity.
The Growing Pains of Success
With a strong order book and rising global interest, the shipyard’s production team found themselves facing a set of persistent challenges:
Fragmented Documentation: Most technical documents, checklists, and certifications were stored across physical folders, email chains, and individual spreadsheets. This made it difficult to track project status, document revisions, or ensure quality assurance steps were being followed consistently.
Inventory Gaps and Delays: The lack of a unified inventory management system often led to delays in production. Critical components were sometimes overlooked in procurement lists or misplaced in storage, creating last-minute scrambles to source parts and verify fit-outs.
Siloed Teams and Communication Breakdowns: With naval architects, project managers, engineers, and subcontractors all working on overlapping phases, the absence of a centralized information flow resulted in repeated tasks, missed updates, and inconsistent timelines.
Warranty Workflows Without Visibility: After delivery, warranty-related communications were tracked manually through spreadsheets and email threads. As warranty claims began to accumulate with each new delivery, it became clear that tracking repairs, assigning tasks, and maintaining service history across yachts was not sustainable without a more organized system.
Production Complexity in Custom Builds
Unlike mass-produced vessels, each catamaran in this shipyard’s portfolio is a unique configuration. Owners often request changes mid-build, from layout adjustments to the integration of new technologies. While this flexibility is a hallmark of the brand, it also means that the documentation for each vessel diverges—creating even more pressure to maintain clear records, consistent workflows, and accurate tracking of changes.
For example, a single change to an electrical routing plan could impact cabinetry, insulation, and other structural elements. If such a modification isn’t properly logged and communicated across departments, it can lead to rework, scheduling delays, or warranty issues after delivery.
Recognizing the Need for Change
As the shipyard scaled up operations to meet growing demand, leadership initiated an internal review of production bottlenecks and after-sales inefficiencies. Several key observations emerged from this process:
Time spent on non-value-adding admin tasks—such as locating files or cross-checking component availability—was steadily increasing.
New project managers and engineers required significant onboarding time, largely because knowledge transfer relied on informal channels and undocumented processes.
Quality control procedures were uneven, with some teams developing personal tracking methods while others relied on verbal handovers.
Warranty cases were difficult to analyze in aggregate due to inconsistent or missing records, limiting their ability to learn from recurring issues.
Starting the Journey Toward Modernization
With these challenges laid bare, the shipyard began taking steps toward digital transformation. This involved:
Mapping their core workflows across design, production, procurement, and after-sales to identify common gaps.
Creating standardized checklists and documentation templates that could be adapted to each vessel without starting from scratch.
Streamlining communication flows between departments, with a particular emphasis on ensuring that production changes are properly reviewed by technical leads and recorded for future reference.
Planning a central knowledge base to store component specifications, installation guides, technical drawings, and historical modifications for each yacht.
Outlining a more structured warranty process with clear task assignments, escalation paths, and service history tracking.
A Culture of Craftsmanship Meets Process Discipline
Crucially, the shipyard’s leadership emphasized that these efforts were not about replacing craftsmanship with rigid automation. Instead, they sought to empower their teams with tools and systems that allow them to focus on what they do best—designing and building exceptional yachts—while reducing the friction and risk caused by outdated administrative practices.
The internal transformation was positioned not as a top-down mandate, but as a collaborative improvement process. Input was gathered from carpenters, engineers, project leads, and even clients to ensure that the evolution of internal systems would support the real-world needs of the shipyard’s unique workflow.
Looking Ahead
While this case study does not detail the final results of the shipyard’s changes, it does offer a powerful look at the kinds of operational pressures faced even by world-class builders. Managing bespoke yacht builds at scale requires more than technical skill—it demands clarity, consistency, and systems that grow with the company.
By acknowledging pain points and proactively redesigning internal workflows, this shipyard took an important first step in aligning their behind-the-scenes operations with the high-performance vessels they are known for delivering. We’re excited to simplify Yacht Management for everyone, through our software, education, and community.
Team Aquator