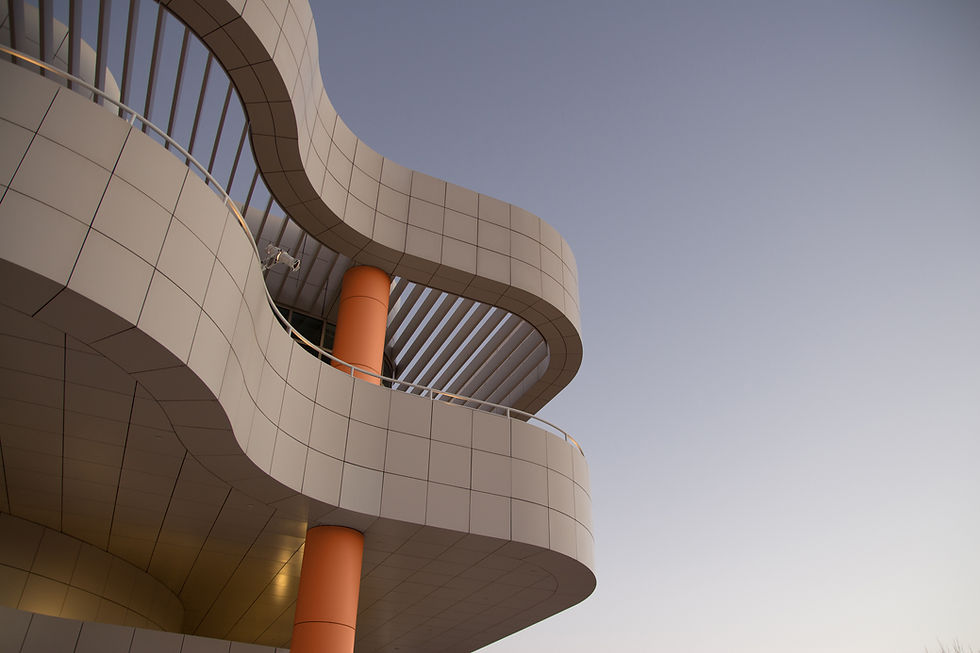
Managing operations on a large superyacht is no small feat. From maintenance logs and safety drills to compliance records and deadline tracking, the complexity increases exponentially with the size and expectations of the vessel. For many years, one 45-meter motor yacht was handling these operations using a traditional paper-based Planned Maintenance System (PMS) and manually maintained ISM/SMS documentation. While this system had served them in the past, it was showing clear signs of strain.
The Operational Struggle
The crew and management team found themselves constantly chasing paperwork. Maintenance tasks were recorded in logbooks and spreadsheets, leaving room for errors, oversights, and lost records. ISM documentation, drills, and compliance logs were maintained in binders, making audits stressful and time-consuming. Deadlines were easy to miss, especially with crew turnover and the seasonal pressure of charters.
The team was committed and experienced, but the system they were using simply couldn’t keep pace with the expectations of a modern superyacht operation.
Making the Switch to a Digital System
In early 2024, the yacht made the decision to adopt a fully digital solution that would bring together its PMS, ISM/SMS documentation, and safety reporting workflows. The objective was to streamline operations, reduce administrative burden, and enable real-time oversight — not just for the crew and management but also for the yacht owner and family office.
The migration process involved:
Digitizing historical maintenance logs and equipment records
Customizing templates and checklists to match existing SOPs
Training onboard crew and shore-based support on the new system
Integrating planned maintenance with the ISM task calendar
Setting automatic alerts for renewals, safety drills, and critical maintenance intervals
Immediate Changes in Workflow
Once the digital systems were operational, the impact was noticeable almost immediately. Engineers could log tasks in real time, schedule upcoming jobs, and track maintenance history — all from a centralized dashboard. Safety drills were recorded and reviewed easily, with built-in verification steps and automated reminders.
The ISM/SMS component created a structured, repeatable workflow that eliminated confusion around what needed to be done, by whom, and when. Documents were stored securely in the cloud, accessible from both onboard systems and shoreside offices.
Improved Oversight and Transparency
Perhaps the most appreciated change came from the ability to share real-time operational updates with the yacht’s owner. From their iPad, the owner could now view ongoing maintenance, safety readiness, and upcoming refit plans — bringing clarity and trust to the operational side of their asset.
This level of visibility fostered a deeper sense of accountability among the team while giving the owner peace of mind that their vessel was operating at the highest standards.
A Platform for the Future
Over the past year, this superyacht has continued to evolve its use of the system. Their success has made them an ideal early adopter for new features and enhancements — including refinements to the PMS module, new ISM form templates, and safety compliance dashboards.
As a result, they now benefit from early access to product developments and direct feedback loops with the platform team. This partnership approach allows them to shape the very tools they use every day.
This case study highlights how even experienced, high-performing crews can be held back by outdated systems. By shifting from paper-based operations to a unified digital platform, the yacht unlocked not just operational efficiency but also greater cohesion between crew, managers, and ownership.
Technology alone doesn’t run a yacht — but when it empowers the people who do, the results can be transformational. We’re excited to simplify Yacht Management for everyone, through our software, education, and community.
Team Aquator